Welding is a critical process in the fabrication of steel structures, ensuring the integrity and strength of the final product. To achieve high-quality welds in steel, adherence to best practices is essential. These practices not only contribute to the structural soundness of the welded components but also enhance safety and efficiency. Here are some key best practices in steel welding:
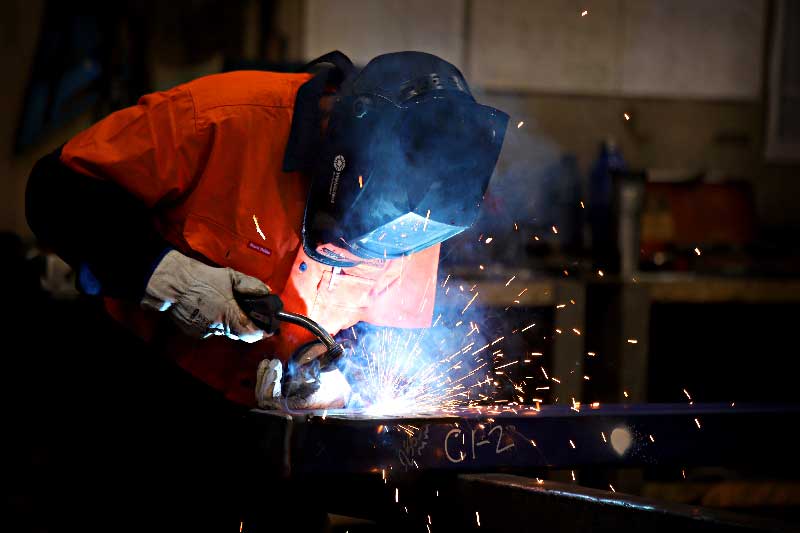
- Proper Welder Training and Certification: Skilled and certified welders are the cornerstone of successful welding projects. Adequate training ensures that welders understand the properties of different steel alloys, welding techniques, and safety protocols. Certification programs validate a welder’s proficiency and competence in the field.
- Thorough Inspection of Materials: Before starting the welding process, it is crucial to inspect the steel materials for defects, contaminants, or inconsistencies. Ensuring the quality of the base materials contributes significantly to the integrity of the final weld.
- Preparation and Cleaning: Cleanliness is paramount in steel welding. Both the welding area and the materials should be free from rust, paint, grease, or any other contaminants that could compromise the weld quality. Proper cleaning and preparation prevent defects such as porosity and inclusions.
- Correct Welding Technique: Employing the appropriate welding technique is vital for achieving strong and durable welds. Techniques such as shielded metal arc welding (SMAW), gas metal arc welding (GMAW), and flux-cored arc welding (FCAW) each have their advantages and are suitable for different applications.
- Controlled Heat Input: Excessive heat can lead to distortion, metallurgical changes, and weld defects. Controlling the heat input is essential for preventing these issues. Welding parameters, such as voltage, amperage, and travel speed, must be carefully adjusted to maintain optimal heat levels.
- Proper Joint Preparation: The design and preparation of the joint have a significant impact on the quality of the weld. Beveling, chamfering, or using other appropriate joint configurations enhances weld penetration and ensures proper fusion between the base metals.
- Effective Welding Positioning: The orientation of the welding joint significantly affects the quality of the weld. Proper positioning minimizes welding defects and ensures the weld metal is deposited where it is needed. Welders should be trained to work comfortably in various positions.
- Post-Weld Heat Treatment (PWHT) when necessary: In some cases, especially with certain steel alloys, post-weld heat treatment may be required to relieve residual stresses and improve the mechanical properties of the weld. Understanding the specific requirements of the steel being welded is crucial in determining whether PWHT is necessary.
- Quality Control and Inspection: Regular inspection during and after the welding process is essential for identifying and rectifying defects promptly. Non-destructive testing methods, such as ultrasonic testing and radiography, can be employed to ensure the integrity of the welds.
- Documentation and Record Keeping: Maintaining detailed records of welding procedures, materials, and inspections is essential for traceability and quality assurance. This documentation aids in troubleshooting any issues that may arise and provides a reference for future projects.
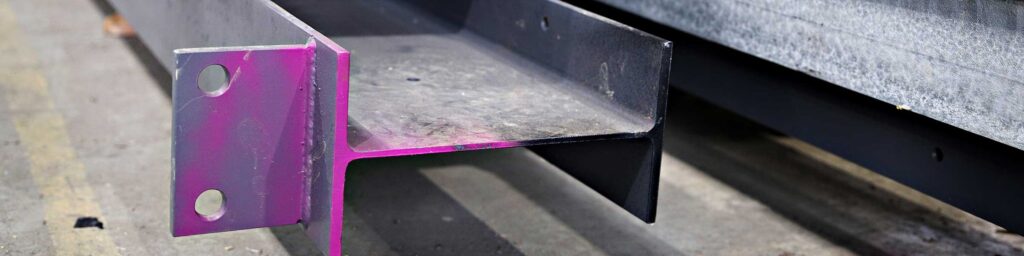
By adhering to these best practices, welders and fabricators can ensure the production of high-quality steel welds that meet structural and safety standards. Continuous training and staying informed about advancements in welding technology also play a crucial role in maintaining excellence in steel welding.